Complete Load Out System for Furnace Dust at Rio Tinto Kennecott Magna, UT
Rio Tinto Kennecott
Magna, UT
General Description
Rio Tinto Kennecott mines essential elements that make modern living possible. Rio Tinto has been a fixture in the Salt Lake Valley for more than 116 years and is the largest private economic driver in Utah. Rio Tinto comprises approximately 11 percent of U.S annual copper production and is one of the largest copper producers in the United States.
Rio Tinto Kennecott collects and stores furnace dust. When the storage silos reach maximum capacity, vacuum trucks haul the material to a reprocessing facility where bulk bags are manually loaded. Jenike & Johanson provided engineering services for flow property testing of the furnace dust and system automation. KWS worked closely with Jenike & Johanson to design a new reliable mass-flow hopper with twin-screw feeder and inclined screw conveyor to reliably store, discharge, meter, and convey the furnace dust to load out.

Maintenance Gates Seal Off Flow in Hopper for Access to Twin-Screw Feeder
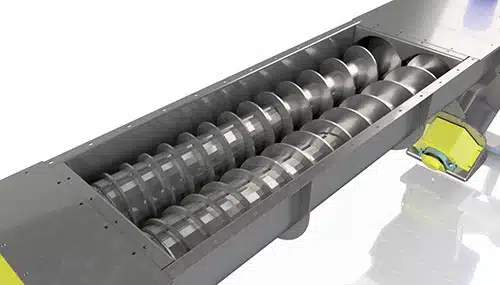
Twin Mass Flow Screws Accurately Meter Furnace Dust
Design Parameters
- Product Type: Furnace Dust
- Material Density: 70 to 90 Lbs. per Cubic Foot
- Capacity: 570 Cubic Feet per Hour
- Duty: Intermittent
KWS Advantages
Jenike & Johanson and KWS have a long-standing, successful relationship and together have solved hundreds of bulk material flow problems. Engineers from Jenike & Johanson and KWS collaborated to create an ideal solution. Because the new equipment fit into an area around existing equipment, 3D models provided by KWS were paramount for a successful installation.
Furnace dust is extremely abrasive, dense, and sluggish to meter. KWS has extensive knowledge and experience with difficult bulk materials such as furnace dust. Bulk materials such as furnace dust are difficult to store and meter due to bridging and ratholing. Working with Jenike & Johanson, KWS provided the hopper and twin-screw feeder using proven mass-flow technologies.
KWS Special Features
The new KWS hopper was designed for a usable volume of 650 cubic feet. The unique conical hopper was designed to prevent material bridging or ratholing after storage at rest. The mass flow hopper transition section ensures uniform flow. “Mass Flow” describes a flow pattern in which all material in a bin is drawn down at the same rate, regardless of if the material is against the sidewall or in the center. Material is drawn down evenly along the entire length of the inlet opening of the screw feeder.
KWS also provided a twin-screw feeder to meter the furnace dust from the hopper to an inclined screw conveyor. Mass flow screws are uniquely designed and manufactured. The mass flow design was developed by Jenike & Johanson and is a combination of variable pitch and tapered inside diameter. A tapered cone is located on the center pipe of the screw from the rear of the inlet opening to approximately the center of the inlet opening. Short pitch flights are mounted on the cone creating available volume for addition of bulk materials from the hopper. Variable pitch is then added to the screw starting where the cone ends and continuing to the discharge.
Drive units are provided for each screw to deliver maximum torque and system redundancy. Screws can operate in-tandem or independently. KWS also provided pneumatically operated maintenance gates between the hopper and screw feeder. The gates can be closed for repair and maintenance purposes.
Load Out System Stores, Meters, and Conveys Furnace Dust
650-Cubic Foot Hopper Utilizes Mass Flow Technology for Accurate Load Out