Classifier Recovers Brass Waste at Mueller Brass Company
General Description
Mueller Brass Company, located in Port Huron, MI manufactures standard and lead-free brass alloys for industrial applications. Alloys and forgings are used for components in many industries including automotive, marine, and industrial transmission. Demand for brass alloys has increased and Mueller needed to increase capacity.
During the manufacturing process, brass bars are finish-ground to specific dimensions. Brass fines are recovered and reused to create more products. The recovery process required a classifier to separate brass from liquids and other solids, clean the brass and return it to the process for reuse. An existing classifier could not keep up with increased capacity. KWS designed and manufactured a classifier to handle the higher capacity and meet the needs of Mueller Brass.
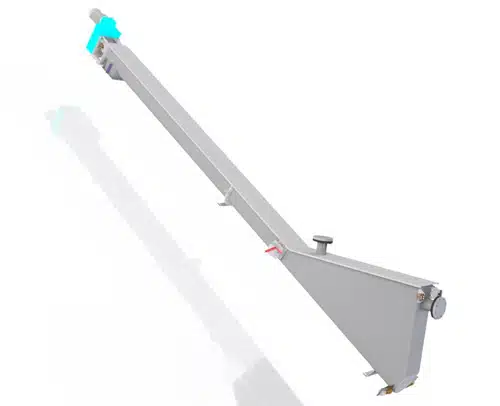
KWS Classifier Separates Brass Fines from Liquids and is Reused
Design Parameters
- Product Type: Brass Powder
- Material Density: 262 Lbs. per Cubic Foot
- Capacity: 10 Cubic Feet per Hour and 50 Gallons per Minute
- Duty: 24 Hours per Day
KWS Advantages
Mueller Brass and KWS worked together to successfully design and manufacture a classifier to produce the desired results. KWS studied the specifications and application to develop a long-term and cost-effective solution. KWS and Mueller Brass coordinated the layout and dimensions, so the classifier fit perfectly without compromising the process or functionality.
KWS designed and manufactured a unique classifier for Mueller Brass using the latest modeling software to ensure proper layout of the grit classifier within the building requirements as well as upstream and downstream equipment. The new KWS classifier fit perfectly with an allowance for maintenance.
KWS Special Features
The discharge screw was located at the bottom of the classifier tank and inclined to remove brass fines from liquid and deliver it to a container. The brass fines are then dried and introduced back into the brass-making process. KWS designed the classifier to operate at a very low speed to allow the fines and liquid to separate. The classifier trough was constructed with a ceramic tile liner for extended wear life. KWS chose a shaftless spiral to convey the fines from the classifier. KWS shaftless spirals are made from the hardest and toughest alloys on the market and designed for many years of continuous operation. The one-piece flanged drive shaft connects the spiral to the drive unit and is guaranteed for the life of the equipment. The volume of the classifier hopper was designed for the flow rate requirements of the application.
Testimonial
"The new KWS Classifier works according to our specifications and expectations. We enjoyed working with the KWS engineering team. KWS was very responsive to our needs."
Bob Kartanys, VP of Engineering – Mueller Brass Company
Inclined Shaftless Spiral Removes Brass Fines from Process
Fines Settle Out of Solution by Gravity
Top View of Shaftless Spiral in Trough
One-Piece Flanged Drive Shaft Connects Spiral to Drive Unit
Classifier Tank is Sized for Additional Flowrate